Introduction
In recent years, as the market’s requirements for the precision of sheet metal parts have increased, precision sheet metal processing has also begun to move to the center of the sheet metal industry.
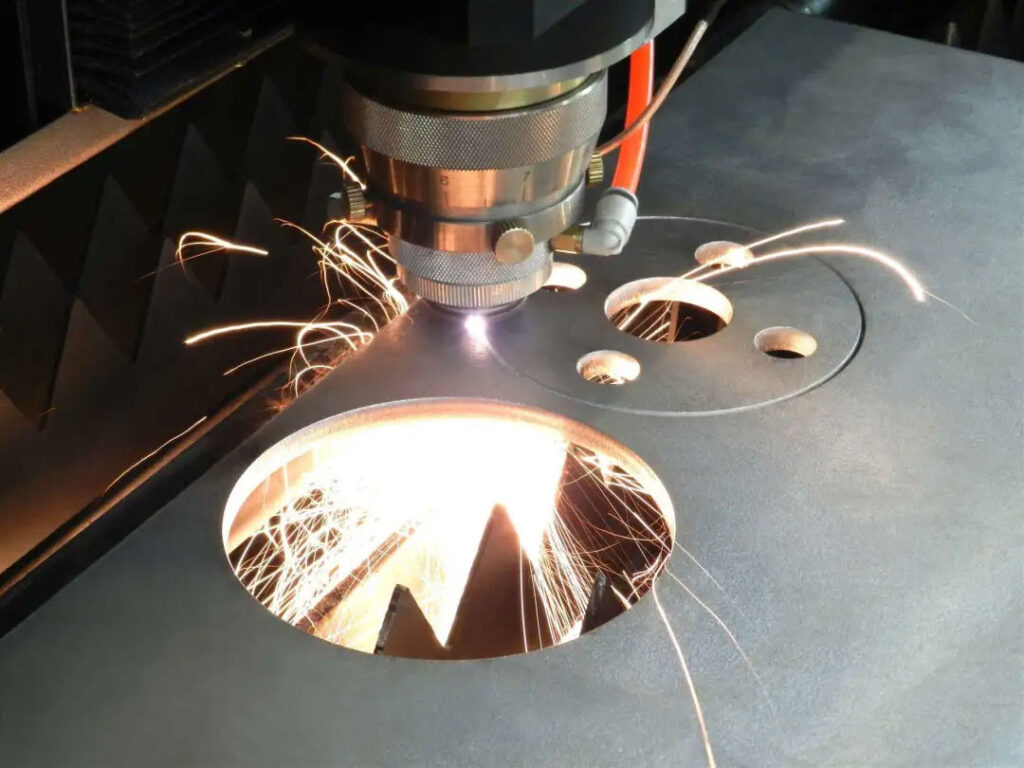
As a key production process in the machinery manufacturing industry, precision sheet metal parts are widely used in rail transportation equipment, precision machine tools, automobile manufacturing, medical equipment, home appliances, etc., and are an important manifestation of China’s intelligent manufacturing. So what is the difference between precision sheet metal processing and ordinary sheet metal processing?
The difference between precision sheet metal processing and ordinary sheet metal processing
From the perspective of development history, precision sheet metal is actually an advanced version of sheet metal processing. There is not much change in the process. The biggest difference is that precision sheet metal processing reduces the precision tolerance range to below 0.2 mm, while the precision of ordinary sheet metal processing is generally between 0.2 and 1 mm.
High-precision sheet metal processing tolerance range: bending: 0-+/-0.1mm; CNC processing: 0-+/-0.1mm; laser cutting 0-+/-0.1mm.
The unwinding and leveling accuracy of precision sheet metal processing can reach 0.3-0.5mm, so sheet metal parts produced by laser/CNC punching/water jet cutting and CNC bending can usually meet the dimensional accuracy requirements.
The sheet metal processing technology has gone through three stages:
From marking with tools such as compasses, scissors, and wooden squares, to hydraulic shears and bending machines that save effort in part processing and have uniform surface quality after processing, to today’s CNC processing equipment . The bending angle of the processed parts can be accurate to 0.1ยฐ, and the size can be accurate to 0.1mm or even higher. There is no need to use trapezoidal lead screws or threads to adjust the positioning little by little or even repeatedly as before, thus saving a lot of time and materials in the manufacturing and production of sheet metal parts.
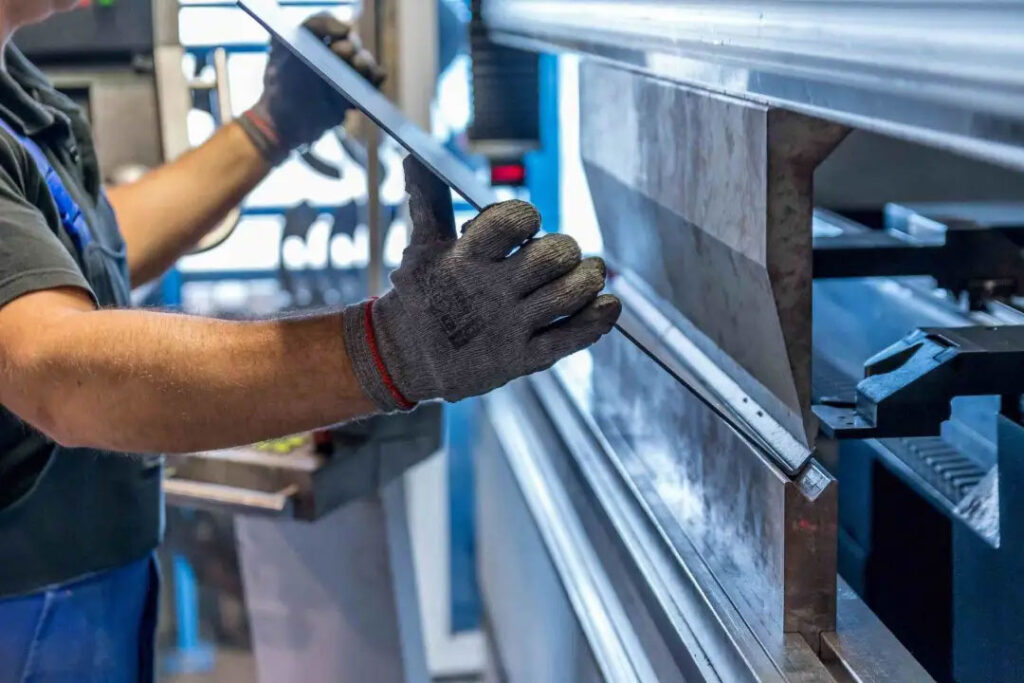
Precision sheet metal processing technology
Precision sheet metal uses high-precision CNC sheet metal equipment, which can realize complex processes that are difficult to achieve with traditional sheet metal processing. Precision sheet metal processing is also suitable for large and small batches of product processing, and has the characteristics of short processing cycle, good uniformity, high processing accuracy, high degree of automation, fast speed, simple and convenient operation, and high efficiency.
Features of Precision Sheet Metal Processing
- The power density of sheet metal processing is high: after the workpiece absorbs the sheet metal processing, the temperature rises rapidly and melts or evaporates. Even materials with high melting point, high hardness and high brittleness can be processed with precision sheet metal;
- Convenient and flexible sheet metal processing: Robots can be used for precision sheet metal processing in harsh environments or places that are difficult for others to access.
- Sheet metal processing is easy to control: it is easy to combine with precision machinery, precision measurement technology and electronic computers to achieve high processing automation and high processing accuracy;
Surface treatment methods for precision sheet metal processing: galvanizing, chrome plating, painting, and electrostatic powder spraying.
Most of the precision sheet metal parts seen on the market have textures on their surfaces. These textures are obtained after surface treatment, which can effectively protect the sheet metal parts from external factors, rust, degeneration, etc.