Introduction
In order to be able to respond sensitively to market changes, many countries developed a new manufacturing technology in the late 1980s, namely the so-called Rapid Prototyping (RP). Different from traditional manufacturing methods, this high-tech manufacturing technology uses a method of gradually increasing materials (such as solidification, bonding, welding, laser sintering, polymerization or other chemical reactions) to form the required part shape, so it is also called Material Increase Manufacturing (MIM).
Rapid prototyping technology integrates the advanced achievements of multiple disciplines such as computers, physics, chemistry, and materials, and solves many problems in traditional processing methods. Different from the material removal method and deformation forming method of traditional mechanical processing, it can form complex parts or molds in one go without the need for special equipment and corresponding tooling, which can be regarded as a leap in human thinking in the manufacturing field. Rapid prototyping technology has broad application prospects in aerospace, mechanical electronics, medical and health fields, has received widespread attention and quickly become a research hotspot in the manufacturing field, and has become an important part of advanced manufacturing technology. This technology has developed rapidly in the late 1990s; in the history of mechanical manufacturing, it has the same important position as the numerical control technology in the 1960s and the non-traditional processing technology in the 1980s.
The principle and main advantages of laser rapid prototyping technology
The basic working principle of rapid prototyping technology is discreteness and accumulation. First, the physical model of the part is converted into a computer electronic model through CAD modeling or a three-dimensional digitizer, and then the CAD model is converted into an STL (stereolithography) file format. The computer three-dimensional solid model is discreted in the z direction using layering software to form a series of thin sheets with a certain thickness. A laser beam (or other energy flow) under computer control is used to selectively solidify or bond a certain area, thereby forming a layer that constitutes the part entity. In this way, a prototype (three-dimensional entity) is gradually accumulated.
If necessary, some post-processing (such as deep curing and grinding) processes are required to make it meet the requirements of functional parts. The recent rapid prototyping technologies mainly include: Stereo Lithography Apparatus (SLA); Selective Laser Sintering (SLS); Laminated Object Manufacturing (LOM); Fused Deposition Modeling (FDM); 3D printing and material removal molding technology.
Since rapid prototyping technology (including laser rapid prototyping technology) only adds materials where they are needed, it is very suitable for CIM, CAD and CAM from the aspects of design to manufacturing automation, from knowledge acquisition to computer processing, from planning to interface and communication, and shows many advantages compared with traditional manufacturing methods.
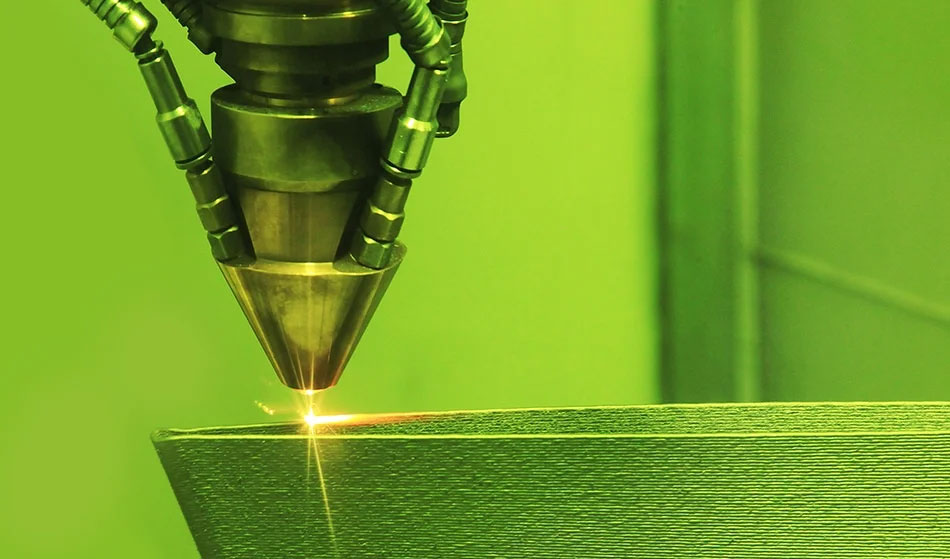
1.Rapidity
Rapidity means that a prototype can be manufactured with the design of a 3D surface or body model of a product. From CAD design to the completion of prototype production, it only takes a few hours to dozens of hours, which is much faster than traditional methods.
2.Suitable for molding complex parts
When using laser rapid prototyping technology to make parts, no matter how complex the parts are, they are broken down by computer into two-dimensional data for molding, without distinction between simple and complex. Therefore, it is particularly suitable for molding parts with complex shapes that are difficult or even impossible to manufacture using traditional methods.
3.Highly flexible
Without the need for traditional processing tools and multiple equipment, parts can be quickly molded into prototypes and parts with certain accuracy and functions on one device. If you want to modify a part, you only need to modify the CAD model, which is particularly suitable for single-piece and small-batch production.
4.Highly integrated
After laser rapid prototyping technology converts CAD data into STL (Standard Transformer for Rapid Prototyping) format[45], the rapid prototyping process can begin. The conversion from CAD to STL files is done automatically in the CAD software. The rapid prototyping process is a two-dimensional operation that can be highly automated and programmed, that is, complex three-dimensional parts can be formed using simple and repetitive two-dimensional operations without the need for special tools or human intervention.
Laser Rapid Prototyping Technology
At present, the method of using laser energy as material binding energy is quite common. In the past 10 years, more than ten kinds of laser rapid prototyping technologies have been developed at home and abroad. The following focuses on the principles, characteristics and applications of several laser rapid prototyping technologies.
1.Stereoscopic light modeling technology
Stereoscopic light modeling technology, also known as light-curing rapid prototyping technology, is one of the earliest commercialized rapid prototyping technologies with the highest market share. Now, this machine has become a popular product. Japan, Germany, Belgium and other countries have invested a lot of manpower and material resources in researching this technology, and products are constantly coming out. Xi’an Jiaotong University in my country has also successfully developed a stereoscopic light modeling machine LPS600A and manufactured parts on it.
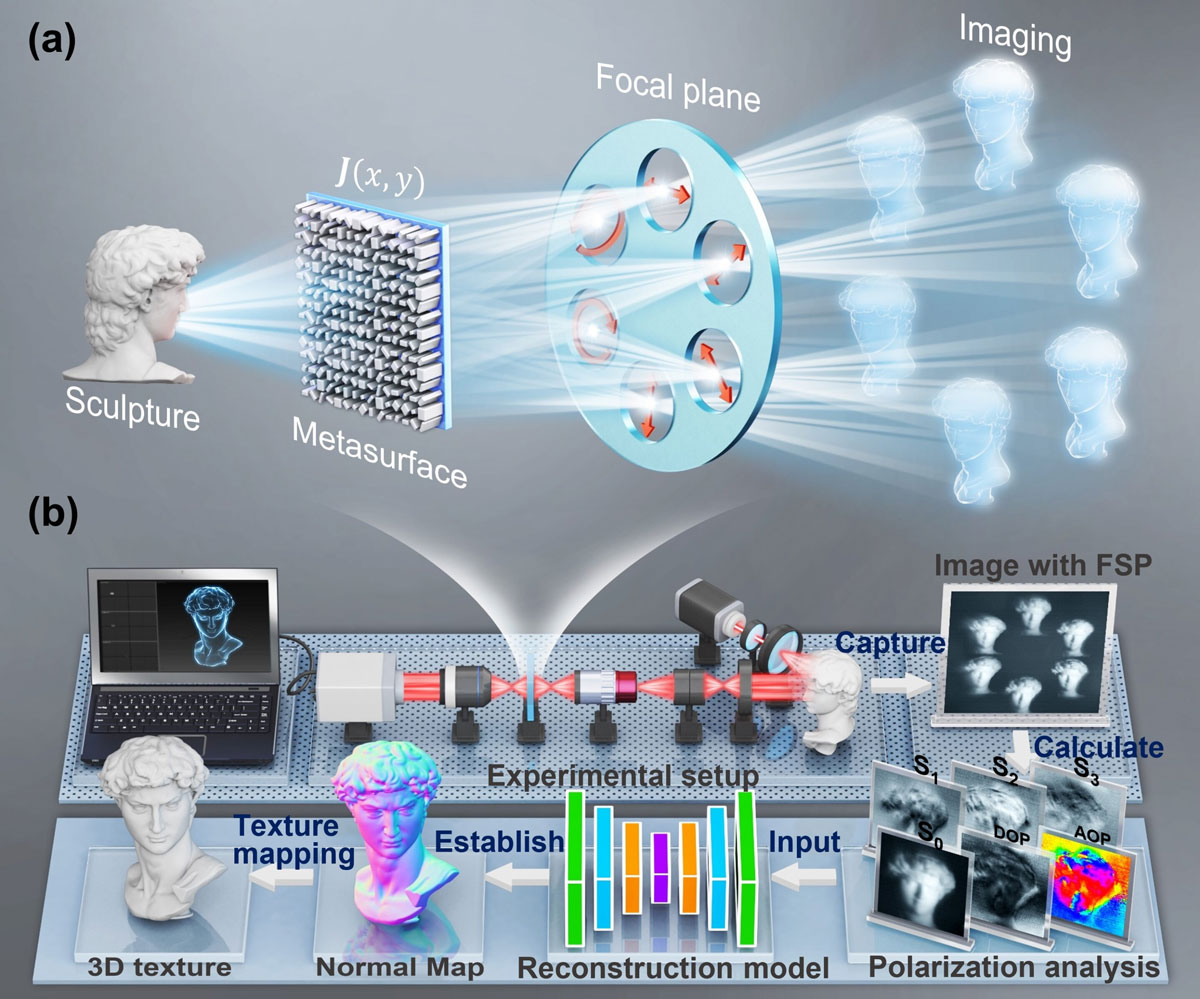
The schematic diagram of the principle of three-dimensional light modeling technology is shown above.
It is a typical layer-by-layer manufacturing method. It uses liquid photopolymer photosensitive resin (polyacrylate, polyepoxy, etc.) as raw materials. Under computer control, the ultraviolet laser scans the surface of the photosensitive resin point by point according to the information of each layered section of the part. The thin layer of resin (about a few tenths of a millimeter) in the scanned area undergoes photopolymerization reaction and solidifies to form a thin layer of the part. After one layer is solidified, the workbench moves down a layer thickness so that a new layer of liquid resin can be applied to the surface of the previously solidified resin, and then the next layer of scanning processing is carried out.
The newly cured layer is firmly adhered to the previous layer, and this process is repeated until the entire prototype is manufactured. Since the photopolymerization reaction is based on the action of light rather than heat, only a low-power laser source is required for operation. In addition, because there is no heat diffusion and the chain reaction can be well controlled, it can be ensured that the polymerization reaction does not occur outside the laser point. Therefore, the processing accuracy is high (ยฑ0.1mm), the surface quality is high, the utilization rate of raw materials is high (close to 100%), the production efficiency is high, and parts with complex shapes (such as hollow parts and molds) and particularly fine parts (such as jewelry, crafts, etc.) can be manufactured. For larger parts, the method of first forming in blocks and then bonding can be used for production.
2.Selective Laser Sintering Technology
Selective laser sintering technology is very similar to stereoscopic light modeling technology. It also uses a laser beam to scan various raw materials, but uses powder materials instead of liquid photopolymers. The basic principle diagram of selective laser sintering technology is shown in Figure 7-30. Under computer control, the CO2 laser beam acts on the powder material (nylon, plastic, metal, ceramic coating powder or powder mixture) on the selected scanning track at a certain scanning speed and energy, selectively melts the powder, and makes the powder bond and solidify to form a layer. The unsintered powder is used as a support material, and then driven by a motor to make the powder consolidation surface drop to a certain height. After a certain thickness of new powder is laid, the above process is repeated until the entire part is formed. Selective laser sintering technology has the characteristics of a wide selection of raw materials, no need for special support, easy cleaning of excess materials, and a wide range of applications. It is suitable for the manufacture of prototypes and functional parts of various materials and multiple uses.
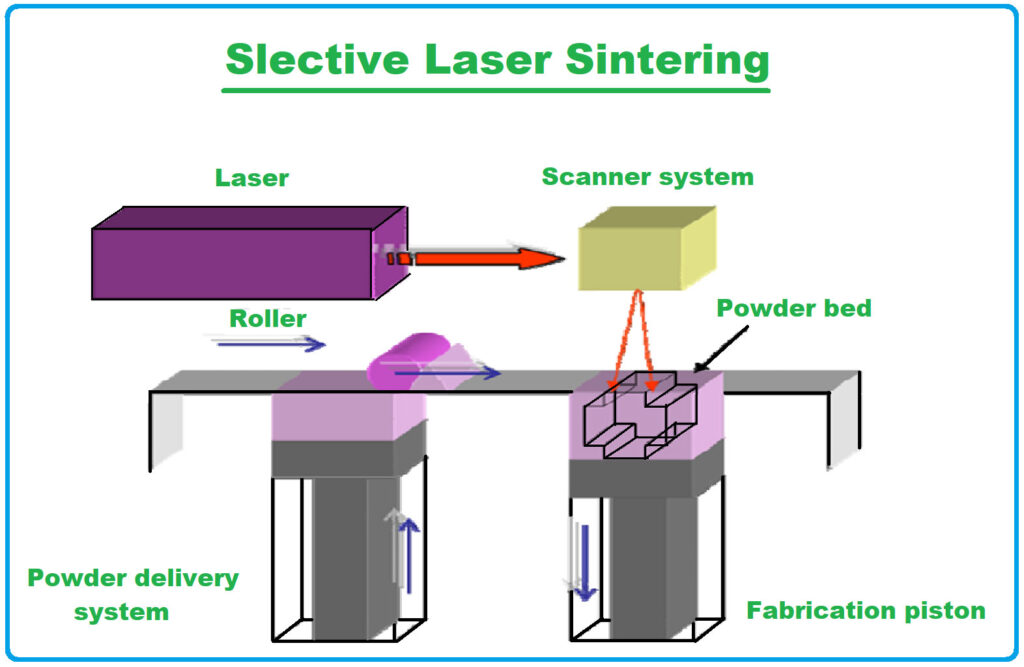
In the process of laser sintering rapid prototyping, the characteristic parameters of the laser (spot size, wavelength, power density) and the scanning speed and scanning interval are very important parameters. These parameters, together with the characteristics of the powder and the sintering atmosphere, are the key factors in laser sintering. The strength of the sintered prototype is a function of the porosity and binder content, and is also affected by the laser scanning path.
Selective laser sintering technology originated from Texas State University in the United States and has been commercialized by DTM in the United States. The third-generation product SLS2000 series developed by the company can sinter various materials such as wax, polycarbonate, nylon, metal, etc. The steel-copper alloy injection mold manufactured by this system can inject 50,000 workpieces. Selective laser sintering is most suitable for the aerospace industry. Because for the aerospace manufacturing industry, the complexity of parts, the diversity of materials, and the degree of difficulty in processing determine that it must adopt the most advanced manufacturing technology in the world today.