Introduction
In the wave of intelligent transformation of manufacturing industry, CNC machining efficiency has become a key indicator of corporate competitiveness.
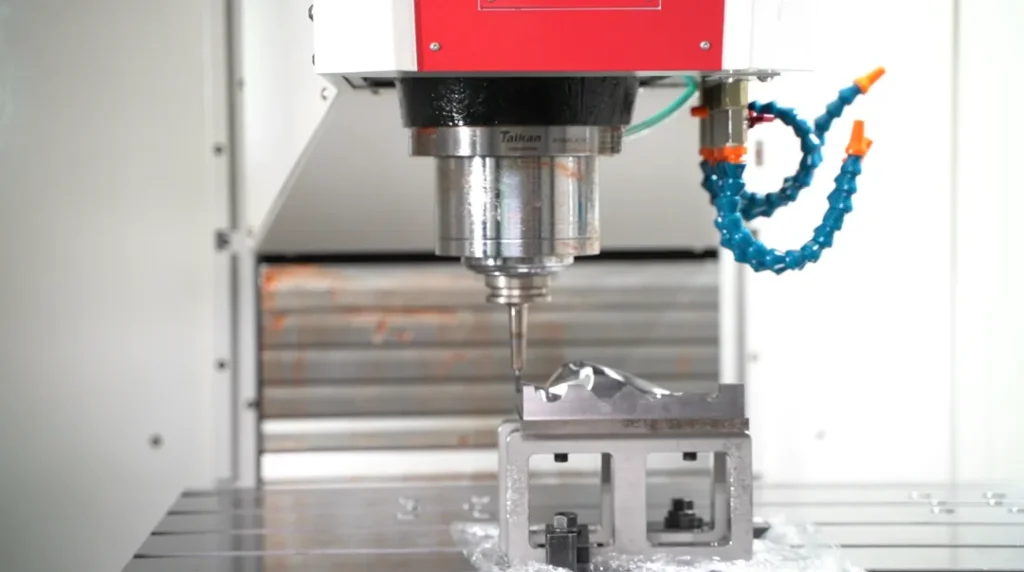
However, in the traditional processing mode, many problems such as time-consuming idle travel and loss during multiple process clamping are common.
Today I will share with you: How to optimize through five directions to improve CNC processing efficiency in technology.
Reasonable division of processing procedures
The division of processes needs to comprehensively consider the part structure and processability, machine tool function, processing content, clamping times, and production organization, and can usually be divided in the following ways:
- Divide by tool concentration: Divide the process according to the tool used. After using the same tool to process all applicable parts on the part, replace the next tool to process the rest. This method can reduce the number of tool changes and unnecessary positioning errors, and shorten the idle time.
- Divide by processing content: According to the structural characteristics of the parts, the processing content is divided into several parts, such as inner cavity, outer shape, curved surface or plane, etc. Usually follow the following principles: (1) Process the plane and positioning surface first, then process the hole.
(2) Process simple geometric shapes first, then process complex geometric shapes.
(3) Process the features with lower precision requirements first, then the features with higher precision requirements. - Classification by roughing and finishing: For parts that are prone to deformation during processing, roughing and finishing are usually treated as different processes because they may be deformed after roughing and need to be corrected.
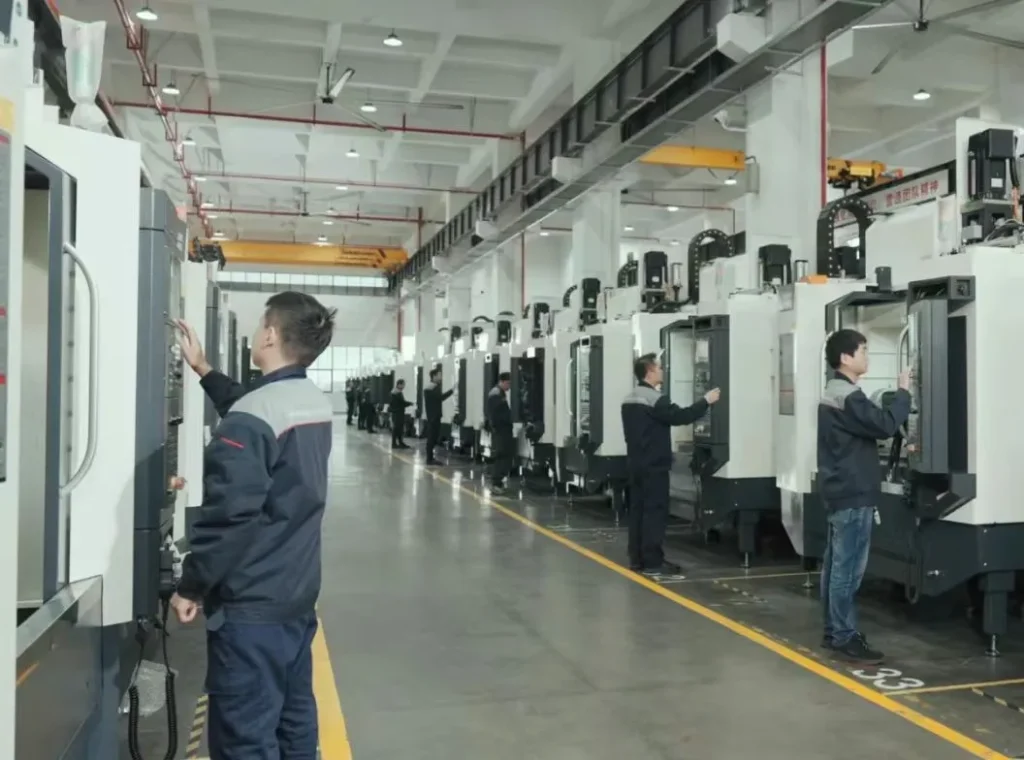
Optimize the processing sequence
- Execute the same positioning, clamping or tooling processes together;
- Complete the internal cavity processing first, then the external shape processing to reduce the damage to the rigidity of the workpiece;
- In the installation of multiple processes, give priority to the process that has less impact on the rigidity of the workpiece;
- The previous process shall not affect the clamping and positioning of the subsequent process, and the interlaced logic of general machine tool processes shall be taken into account.
Optimize the workpiece clamping method
- One-time clamping technology: Use four-axis/five-axis equipment, such as the Taiqun Precision Machinery T-500U five-axis drilling and milling machining center , to complete multi-faceted processing in one clamping through a rotating worktable (for example, box parts can reduce clamping by 3 times);
- Choose the right fixture: give priority to hydraulic/pneumatic fixtures, modular combination fixtures, vacuum suction cups and other fast clamping methods. Evaluate the use of multi-station fixtures to clamp and process multiple identical workpieces at one time.
- Optimize positioning datum: Design reasonable, easy-to-align and stable positioning datum (surface, hole, pin) to reduce alignment time and improve repeated positioning accuracy.
- Consider flexible tooling: For small batches and multiple varieties, consider a flexible fixture system (such as a zero-point positioning system) to achieve rapid switching of workpieces.
- Simplify operation: Minimize the number of adjustment steps and fasteners required for clamping.
Optimize tool point settings and tool paths
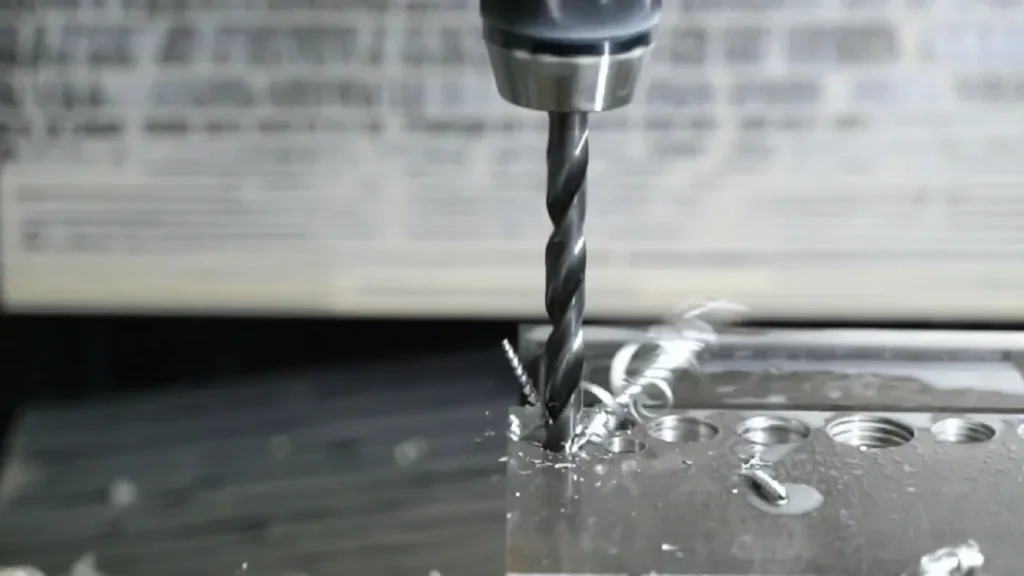
1.Optimize tool setting point
(1) The tool reference point must be the reference position or a part that has been finely machined.
(2) Four principles for selecting tool points: easy to align; easy to program; small tool setting error; easy to check during processing.
(3) When machining with multiple tools, set a unified tool reference point to avoid repeated tool setting.
2.Optimize tool paths
(1) Reduce idle travel: When programming, optimize the toolโs feed, retract, and tool change paths to avoid unnecessary โgoing in circlesโ.
(2) Adopt efficient cutting strategies: such as high-speed cutting, high-cutting depth/small-feed powerful cutting (depending on the capabilities of the machine tool and tool), trochoidal milling, dynamic milling, etc., to make full use of tool performance and improve material removal rate.
(3) Optimize cutting parameters: Under the premise of ensuring tool life and processing quality, find the optimal combination of cutting speed, feed rate and cutting depth through experiments or software simulation.
(4) Utilize tool compensation: Reasonably use tool radius compensation and length compensation to simplify programming and adapt to tool wear.