The rapid prototyping processes that have always been dominant in the rapid field mainly include:ย FDMย ,ย SLAย ,ย SLSย andย LOMย , and these processes have their own advantages. Let’s take a look at the advantages and disadvantages of these processes:
FDM
The Fused Deposition Modeling ( FDM ) rapid prototyping process is a method that does not rely on laser as a molding energy source, but heats and melts various wire materials (such as engineering plastics ABS , polycarbonate PC , etc.) and then deposits them for molding. It is referred to as FDM .
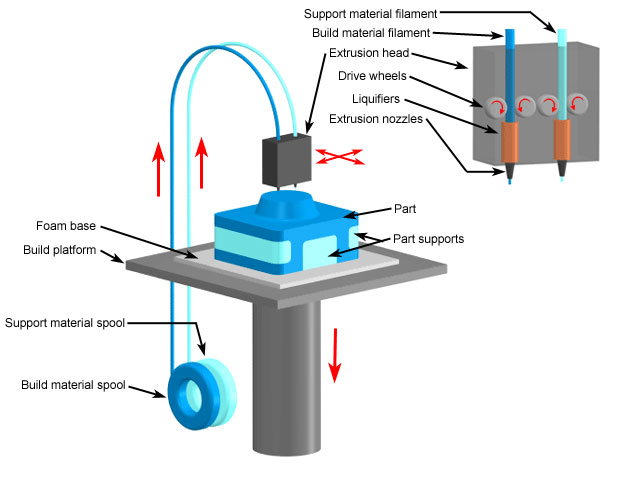
The principle of selective cladding of filamentary materials is as follows: the heating nozzle moves in the XY plane under the control of the computer according to the cross-sectional profile information of the product parts. The thermoplastic filamentary material is sent to the hot melt nozzle by the wire feeding mechanism, and is heated and melted into a semi-liquid state in the nozzle, and then extruded and selectively coated on the workbench. After rapid cooling, a thin sheet profile of about 0.127mm thick is formed. After one layer of cross-sectional molding is completed, the workbench drops a certain height, and then the next layer of cladding is carried out, as if ” drawing ” the cross-sectional profile layer by layer, and this cycle eventually forms a three-dimensional product part.
This process also has a variety of materials to choose from, such as engineering plastics ABS , polycarbonate PC , engineering plastics PPSF , and mixtures of ABS and PC . This process is clean, easy to operate, does not generate garbage, and can be safely used in office environments without the risk of generating toxic gases and chemical pollution. It is suitable for conceptual modeling of product design and product shape and function testing. ABS-i , a material specially developed for medical use, has good chemical stability and can be sterilized by gamma rays and other medical methods, making it particularly suitable for medical use.
The advantages of FDM rapid prototyping technology are:
- The manufacturing system can be used in an office environment without pollution from toxic gases or chemicals;
- One – step forming, easy to operate and no waste generated;
- Unique water-soluble support technology makes it easy to remove the support structure, and can quickly build bottle-shaped or hollow parts and one-time assembly structural parts ;
- Raw materials are provided in the form of rolls, which are easy to carry and quickly replace;
- A variety of materials are available, such as engineering plastics ABS , PC , PPSF and medical ABS in various colors;
The disadvantages of FDM rapid prototyping technology are:
- The molding accuracy is lower than that of foreign advanced SLA technology, with the highest accuracy of 0.127mm;
- The surface finish of the molding is not as good as that of the advanced SLA process abroad;
- The molding speed is relatively slow;
SLA
Selective curing of photosensitive resin is a process based on the principle of stereolithography (SLA) , which is one of the earliest rapid prototyping technologies.
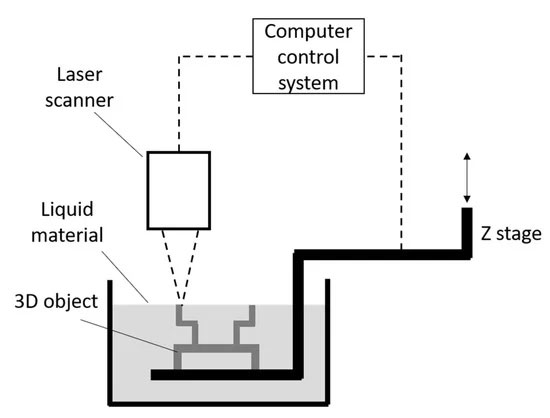
The resin tank is filled with liquid photosensitive resin, which will cure quickly under the irradiation of the ultraviolet laser beam. At the beginning of the molding process, the liftable workbench is at a height of one section layer thickness below the liquid surface. The focused laser beam, under the control of the computer, scans along the liquid surface according to the requirements of the cross-sectional profile, so that the resin in the scanned area is cured, thereby obtaining a resin sheet with the cross-sectional profile. Then, the workbench descends to the height of one sheet, and the cured resin sheet is covered by a new layer of liquid resin so that the second layer of laser scanning and curing can be carried out. The newly cured layer is firmly bonded to the previous layer, and this is repeated until the entire product is formed. Finally, the lifting platform rises out of the liquid resin surface, takes out the workpiece, and performs cleaning, support removal, secondary curing, and surface finishing.
Photosensitive resin selective curing rapid prototyping technology is suitable for making small and medium-sized workpieces, and can directly obtain resin or similar engineering plastic products. It is mainly used for prototyping of conceptual models, or for simple assembly inspection and process planning.
The advantages of SLA rapid prototyping technology are:
- Good surface quality;
- The molding accuracy is high, with an accuracy of 0.1mm (the domestic SLA accuracy is between 0.1-0.3mm , and there is a large fluctuation);
- The system resolution is high;
Technical disadvantages of SLA rapid prototyping:
- A dedicated laboratory environment is required, and the molded parts require post-processing, such as secondary curing, moisture-proof treatment and other processes.
- Poor dimensional stability. As time goes by, the resin will absorb moisture in the air, causing warping and deformation of the soft and thin parts, which will greatly affect the overall dimensional accuracy of the molded parts;
- The life of the helium – cadmium laser tube is only 3,000 hours, and the price is relatively expensive. Since the entire cross section needs to be scanned and solidified, the molding time is long, so the production cost is relatively high.
- The types of materials available are limited and must be photosensitive resins. Workpieces made of this type of resin cannot be tested for durability and thermal properties in most cases, and photosensitive resins pollute the environment and cause skin allergies .
- It is necessary to design the support structure of the workpiece to ensure that each structural part produced during the molding process can be reliably positioned. The support structure needs to be removed manually when it is not fully solidified, which can easily damage the molded part.
SLS
Selective Laser Sintering ( SLS ) is a rapid prototyping process.
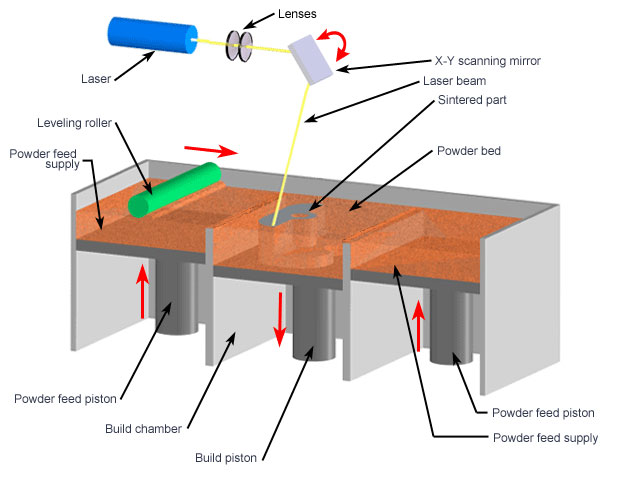
Selective sintering of powder materials uses a carbon dioxide laser to selectively sinter powder materials (mixed powders of plastic powders and binders, etc.). It is a rapid prototyping method that stacks discrete points layer by layer into a three-dimensional entity.
Selective sintering of powder materials uses a carbon dioxide laser to selectively sinter powder materials (plastic powder, mixed powder of ceramics and binder, mixed powder of metal and binder, etc.). It is a process method that integrates three-dimensional entities layer by layer from discrete points.
Before starting processing, the nitrogen-filled studio is heated and kept at a temperature below the melting point of the powder. During molding, the feed barrel rises and the powder-laying roller moves. A layer of powder material is first laid on the work platform. Then, the laser beam sintered the powder in the solid part according to the cross-sectional contour under computer control, so that the powder melted and then formed a layer of solid contour. After the first layer of sintering is completed, the workbench descends to the height of a cross-sectional layer, and another layer of powder is laid, and the next layer is sintered. This cycle forms a three-dimensional prototype part. Finally, after cooling for 5-10 hours, the part can be removed from the powder cylinder. The unsintered powder can support the workpiece being sintered. When the sintering process is completed, the part is removed. The selective sintering process of powder materials is suitable for molding small and medium-sized parts, and can directly produce plastic, ceramic or metal parts. The warping deformation of the parts is smaller than that of the selective curing process of liquid photosensitive resin. However, this process still requires scanning and sintering of the entire cross section, and the studio needs to be heated and cooled, so the molding time is relatively long. In addition, due to the limitations of powder particle size and laser points, the surface of the part is generally porous. After the mixed powder of ceramic, metal and binder is sintered and the prototype part is obtained, it must be placed in a heating furnace to burn out the binder and infiltrate the filler into the pores, and the subsequent processing is complicated.
The selective sintering rapid prototyping process of powder materials is suitable for visualizing product design and making functional test parts. Since it can use metal powders of various compositions for sintering and post-processing such as copper infiltration, the products made from it can have mechanical properties similar to those of metal parts. However, due to the rough molding surface and complex processes such as copper infiltration, it needs to be further improved.
The advantages of SLS rapid prototyping technology are:
- Compared with other processes, it can produce harder molds;
- A variety of raw materials can be used, including engineering plastics, wax, metal, ceramics, etc;
- The construction time of parts is short and can reach 1in/h;
- No need for design and construction support;
The disadvantages of SLS rapid prototyping technology are:
- There is laser loss and a special laboratory environment is required, and the cost of use and maintenance is high;
- Preheating and cooling are required, and post-processing is troublesome;
- The molding surface is rough and porous, and is limited by the powder particle size and laser spot;
- The processing chamber needs to be continuously filled with nitrogen to ensure the safety of the sintering process, and the processing cost is high;
- The molding process produces toxic gases and dust, polluting the environment;
LOM
Laminated Object Manufacturing (LAM ) rapid prototyping technology is a thin film material stacking process, referred to as LOM.
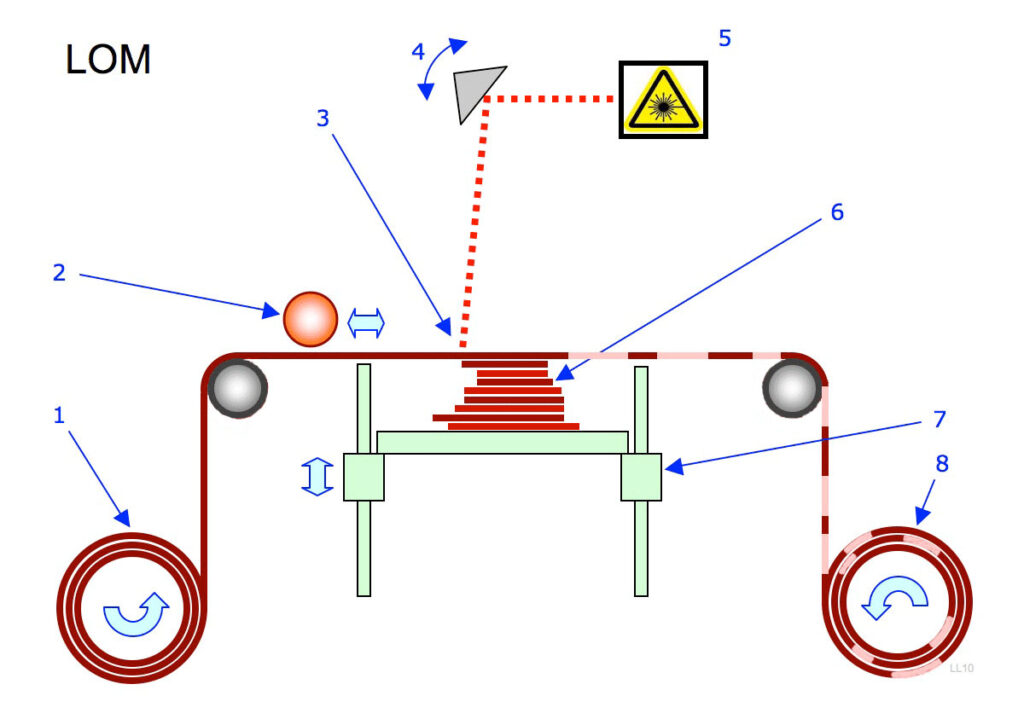
The production of foil laminated entities is based on the contour lines of each section of the 3D CAD model. Under computer control, the laser cutting system is instructed to move the cutting head in the X and Y directions. The feeding mechanism delivers the foil (such as coated paper, coated ceramic foil, metal foil, plastic foil) coated with hot melt adhesive to the top of the workbench. The laser cutting system uses a carbon dioxide laser beam to cut the paper on the workbench along the contour line according to the cross-sectional contour extracted by the computer, and cuts the non-contour area of โโthe paper into small pieces.
Then, the layers of paper are pressed and bonded together by the hot pressing mechanism. The lifting table supports the workpiece being formed and lowers a paper thickness after each layer is formed to feed, bond and cut a new layer of paper. Finally, a three-dimensional prototype part surrounded by many small waste pieces is formed. Then it is taken out and the excess waste pieces are removed to finally obtain a three-dimensional product.
The rapid prototyping process of laminated solid is suitable for making large and medium-sized prototypes, with small warping deformation, short molding time, long laser service life, and good mechanical properties of the finished parts. It is suitable for conceptual modeling and functional testing parts of product design. And because the finished parts have wood properties, they are particularly suitable for direct production of sand casting molds.
The advantages of LOM rapid prototyping technology are:
- The forming speed is fast. Since the laser beam only needs to cut along the contour of the object without scanning the entire cross section, the forming speed is very fast, so it is often used to process large parts with simple internal structures;
- No need to design and build support structures;
The disadvantages of LOM rapid prototyping technology are:
- There is laser loss, and a special laboratory environment is required, and the maintenance cost is high;
- There are relatively few types of raw materials that can be used in practice. Although several raw materials can be selected, such as paper, plastic, clay and synthetic materials, only paper is commonly used at present, and other foils are still under research and development;
- Moisture-proof treatment is required. Paper parts are easy to absorb moisture and deform, so they must be immediately treated with resin, moisture-proof paint, etc. after molding;
- It is difficult to construct parts with fine shapes and multiple curved surfaces, and is limited to parts with simple structures;
- It is difficult to remove waste, so this process is not suitable for building parts with complex internal structures;
- Fires often occur when the temperature in the processing room is too high. Therefore, full-time personnel are required to be on duty during the work process;