Introduction
Sheet metal processing allows the use of a combination of various techniques and compatible materials to create different products. Therefore, the popularity of sheet metal fabrication technology shows its importance in a wide range of applications. However, it is essential to understand how this process works so that you can use it to your advantage.
This article explores the basics of sheet metal fabrication, describing the techniques involved and their applications. You will also learn about the various advantages of the process and the materials that are suitable for metal fabrication processes.
What is Sheet Metal Fabriction?
Sheet Metal Fabriction is the process of converting flat metal into metal structures or products through cutting, punching, bending, welding and assembly. Sheet metal can be made into almost any shape by cutting, bending or stretching, which is usually achieved by cutting and heating the metal.
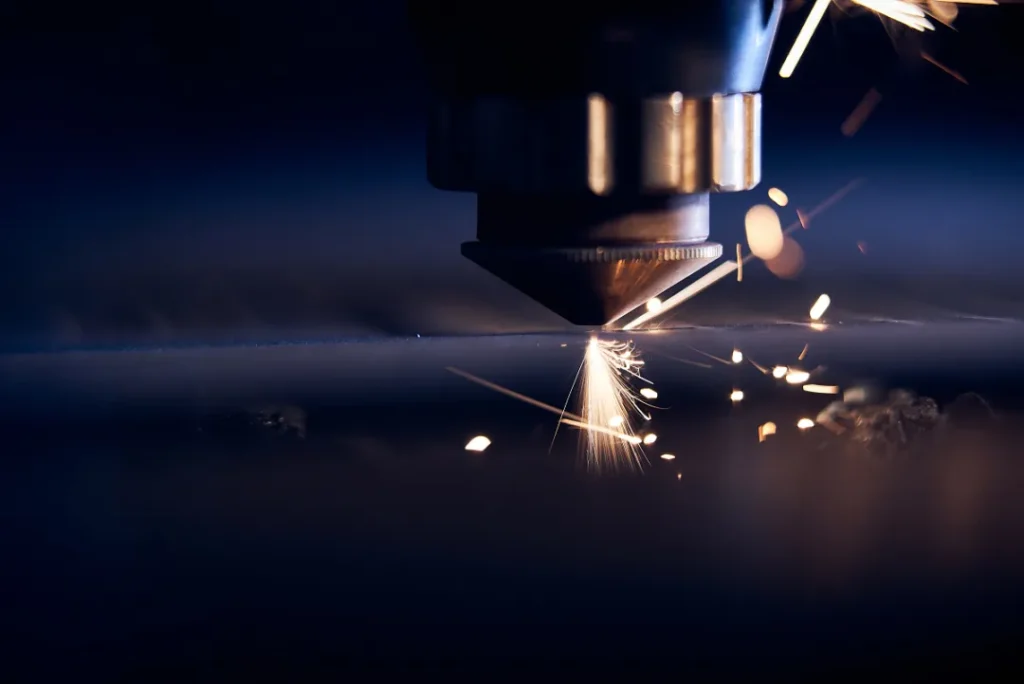
In sheet metal manufacturing, press brakes are often used to assist in the precise bending and forming of metal. There are various types of press brakes on the market, each with special features and used for different purposes.
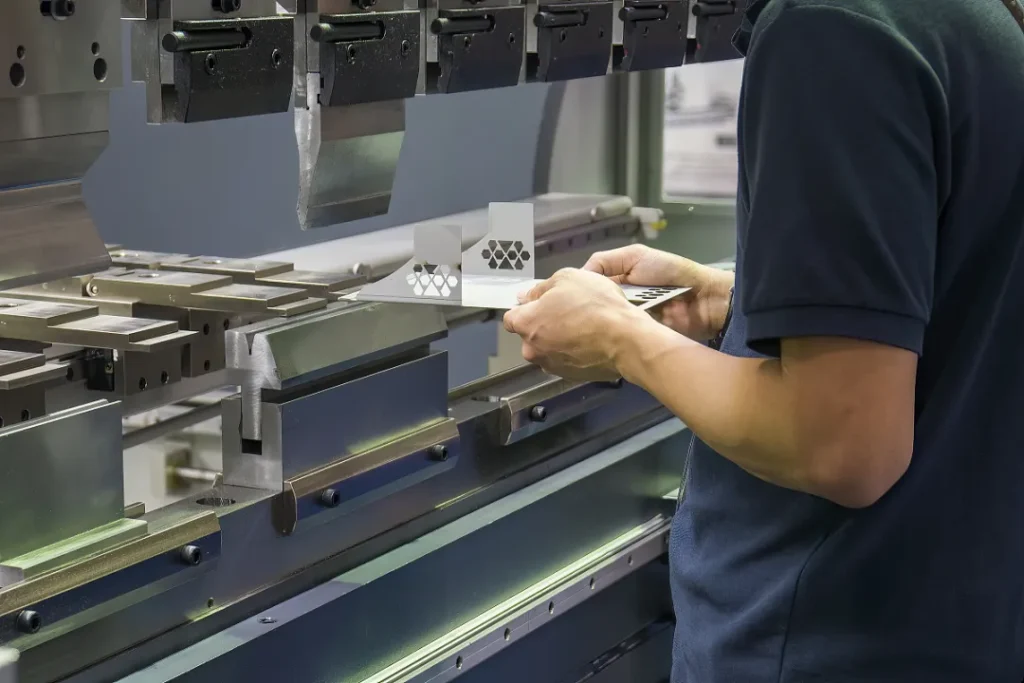
Another major step in sheet metal manufacturing is welding. Once all the parts are made, they are welded together. To prevent warping or other anomalies, we use a variety of welding techniques, such as sanding the metal during cooling, staggering welds, and using fixtures.
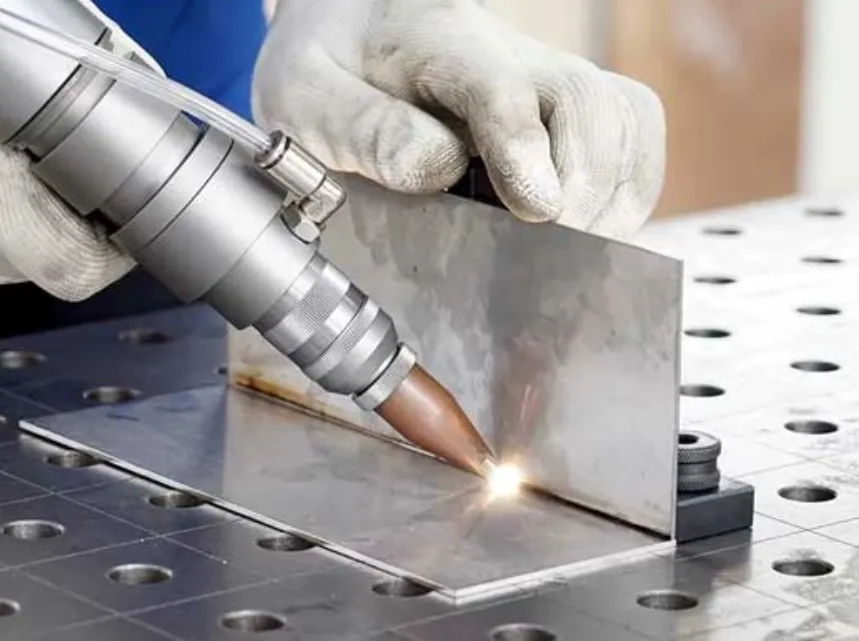
Metal products generally undergo surface treatments such as sandblasting, powder spraying, oxidation, and polishing to ensure the beautiful appearance of the metal products. After the surface treatment is completed, the products can be sent to customers.
What processes does Sheet Metal Fabriction include?
Sheet Metal Design
Sheet metal design is the process of processing metal sheets into various complex shapes through shearing, bending, stamping and other processes. During the design process, material selection, structural strength and production process need to be considered to ensure product durability and manufacturing efficiency. In addition, accurate drawings and 3D models are the key to success and can effectively reduce production errors and costs.
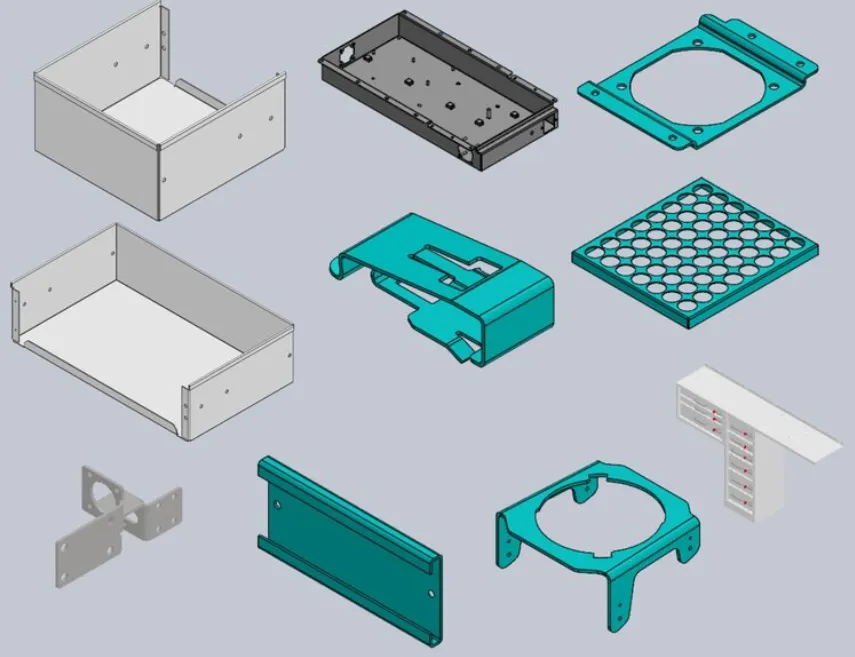
Laser Cutting
Sheet metal laser cutting involves using a focused laser beam to melt metal in a localized area. Laser cutting machines are compatible with a wide range of metals, from non-ferrous metals to mild and stainless steels. The technology consists of two sub-processes that run simultaneously. The first involves focusing a high-powered laser beam on a sheet of metal. The material absorbs the thermal energy of the laser beam, causing it to vaporize. Meanwhile, the second process involves the cutting nozzle providing a gas blow for the laser cutting. This gas is typically oxygen or nitrogen. It helps protect the processing head from spatter and steam during sheet metal fabrication projects.
Plasma cutting
Plasma cutting is a thermal cutting process for metal using an ionized gas called plasma. This method uses a lot of heat to cut the metal, which creates large burrs and oxidation zones near the cutting area. In addition, it allows for faster cutting, high accuracy, and repeatability in sheet metal fabrication. Plasma cutting tools work effectively only on conductive metal sheets. Therefore, it is one of the most suitable methods for cutting conductive materials of medium aluminum thickness.
Water jet cutting
The cutting process involves using a high-pressure stream of water to cut through the metal sheet. Water jet cutting is very versatile and can cut a variety of hard and soft materials using pressurized water and abrasives. It is ideal for cutting soft materials, metal foils , fabrics, or rubber. It is also suitable for cutting hard materials such as copper, carbon steel, aluminum, carbon steel, etc. The pressure involved is usually around 60,000 psi, providing a speed of 610m/s to cut different types of metal sheets. However, water jet cutting is a better alternative to laser cutting technology.
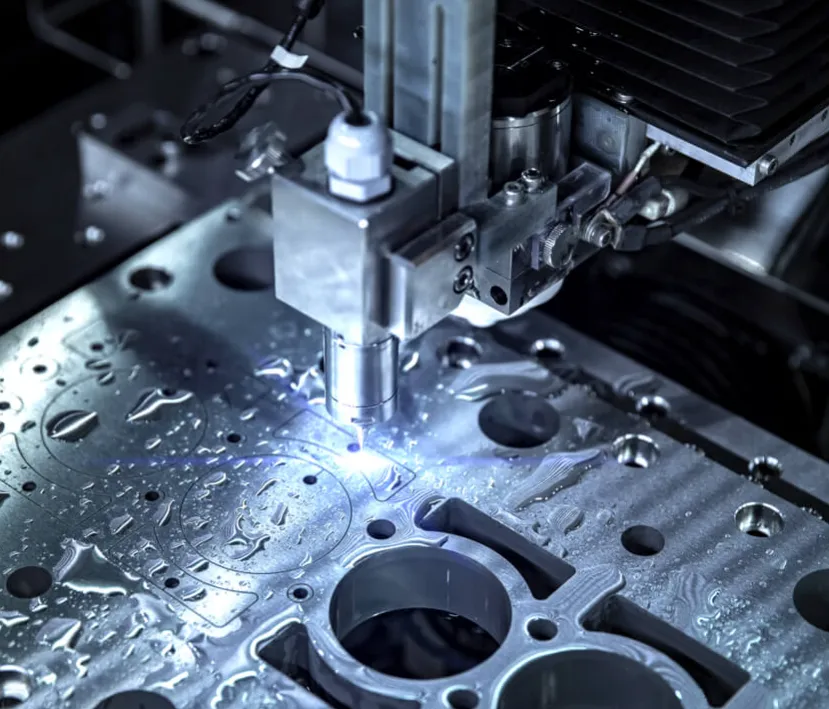
Sheet Metal Bending
Sheet metal bending is highly cost-effective in the production of small batches of prototype products. It involves deforming the metal surface with force and bending it to the required angle to form the desired shape. You can use a bending machine and a rolling machine to do this.
Curl
Plate rolling is a general process that uses work rollers to continuously bend the plate at three points to bend the plate into shape. It can be rolled into workpieces of different shapes such as cylindrical parts and conical parts. The plate rolling machine is based on the principle of three points forming a circle. It uses the relative position change and rotational motion of the workpiece to make the plate produce continuous plastic deformation to obtain a workpiece of a predetermined shape.
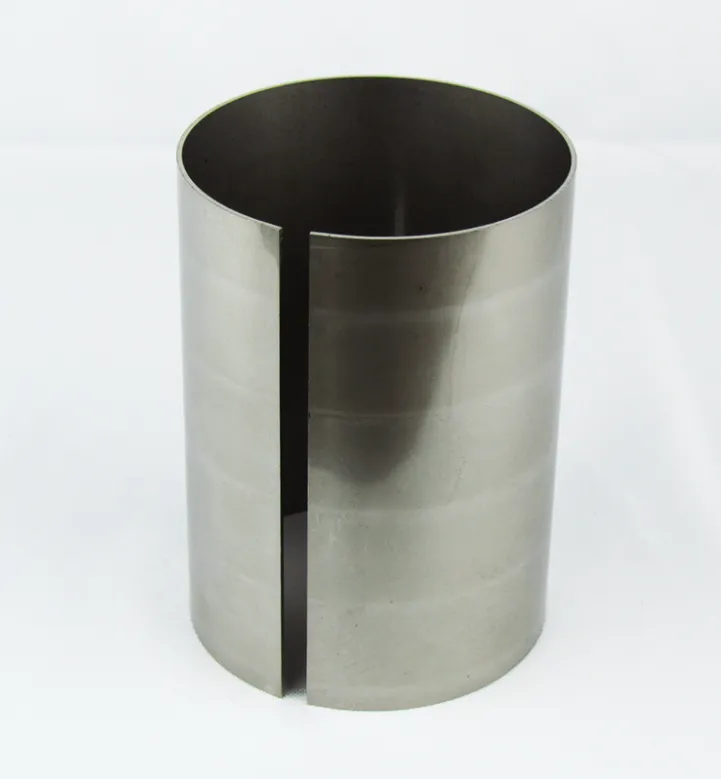
Sheet Metal Welding
MIG welding Metal inert gas shielded welding (MIG)uses a continuous solid wire and shielding gas to prevent atmospheric pollutionApplicable to aluminum, steel and stainless steelWidely used in automobiles and home decoration, cost-effective
TIG welding uses a non-consumable tungsten electrode and an inert gas (argon or helium).It is suitable for non-ferrous metals such as aluminum, titanium, copper, and nickelIt is often used in the aviation and aerospace industries and is suitable for delicate work.
Stick welding Shielded metal arc welding uses a flux-covered electrode as an electrode and does not require shielding gas. It is suitable for hard metals such as steel. The equipment is portable and is often used in construction, shipbuilding and steel manufacturing.
Plasma arc welding is similar to TIG welding, using a tungsten electrode and a small arc to form a hot plasma, working at high speeds, and producing precise welds. It is widely used in the aviation and marine industries.
Electron beam and laser welding use laser and electron beam as heat source High precision, suitable for complex operations Suitable for carbon steel, titanium, stainless steel and aluminum Good-looking output, reducing post-processing.
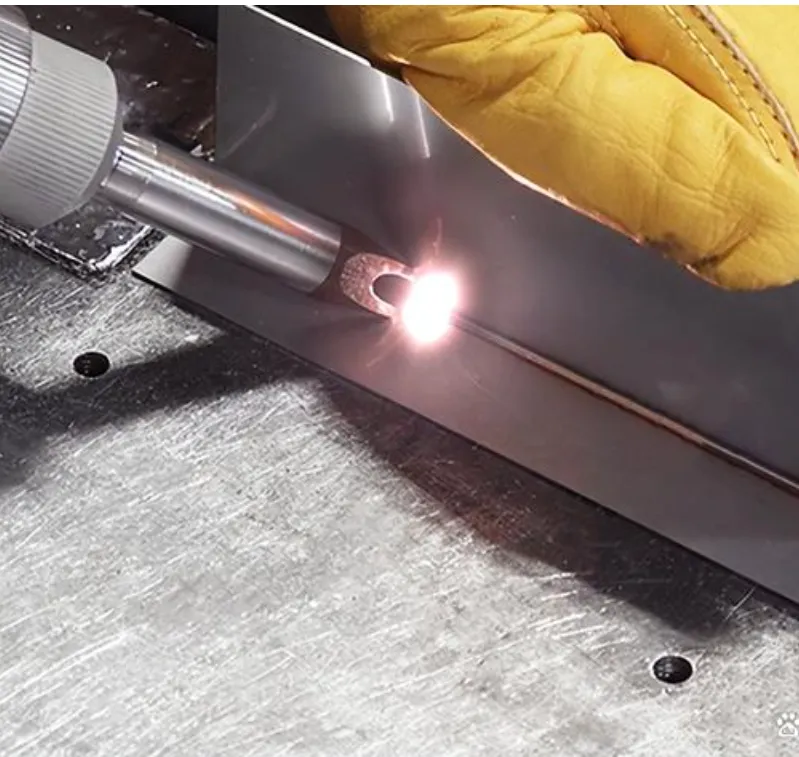
Sheet metal processing post-processing method
Brushed
Sheet metal wire drawing is to place the material between the upper and lower reels of the wire drawing machine. The reels are attached with sanding belts. The material is driven by a motor to pass through the upper and lower sanding belts, leaving traces on the surface of the material. The thickness of the traces varies depending on the sanding belts. The main function is to beautify the appearance. Generally, aluminum materials are considered to use wire drawing as a surface treatment method.
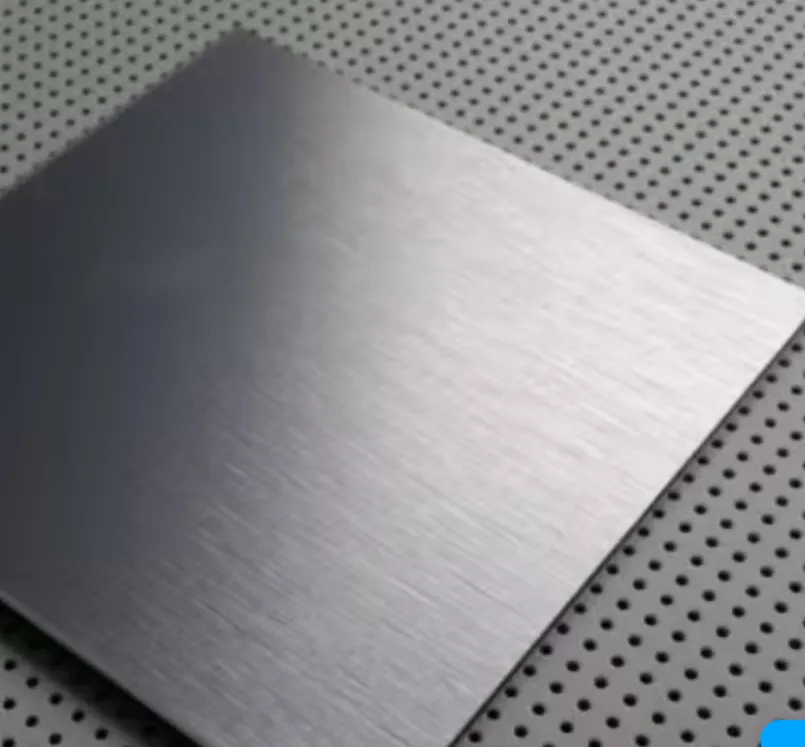
Sandblasting
The wind force of the sandblasting machine is used to blow sand particles onto the surface of the workpiece, forming a dense layer of pits on the surface of the workpiece. The main function is to remove dirt on the surface of the workpiece, increase the adhesion of the workpiece surface, and prepare for subsequent surface treatment methods.
Paint, powder coating
The most well-known is the car paint.
Spraying a layer of paint of various colors on the surface of the material by spraying, high temperature baking, etc., is used to beautify the appearance and increase the corrosion resistance of the material. It is a common surface treatment method. Generally, there are two types of liquid baking paint and powder baking paint, among which powder baking paint is the most common. The baking paint surface is not conductive. Baking paint is not allowed in areas with EMC requirements.
Technical indicators: color difference, film thickness and glossiness.
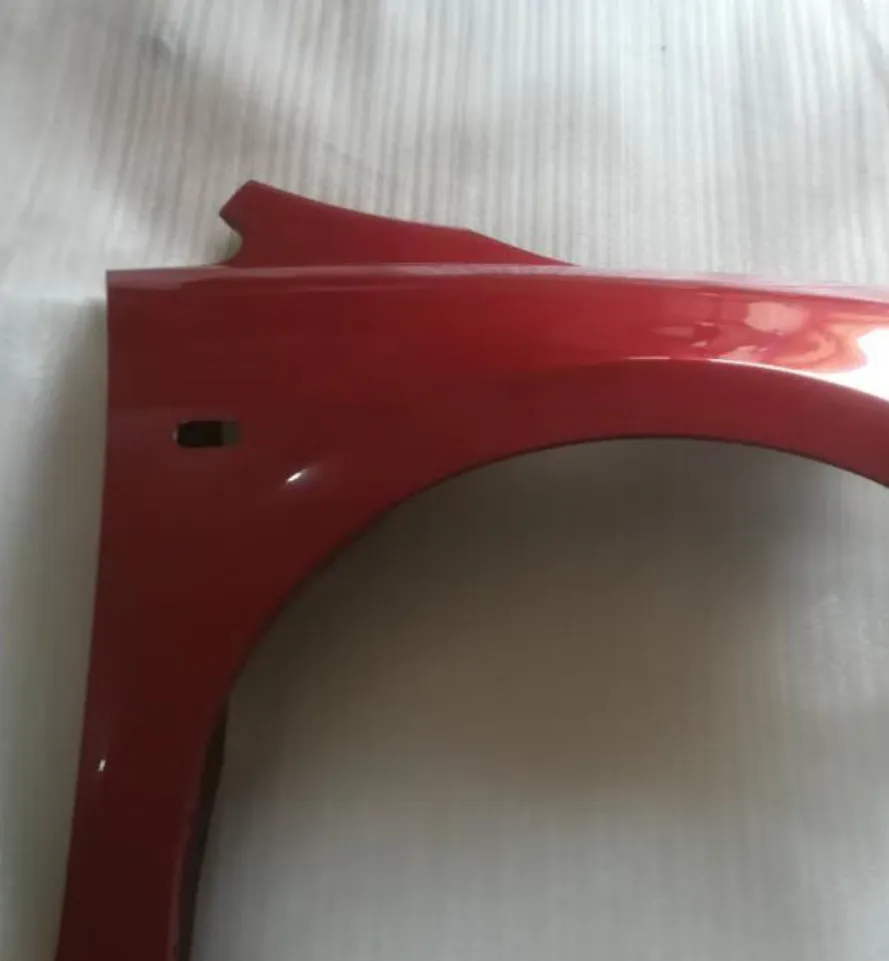
Plating
Through chemical reaction, a layer of other metal is attached to the surface of the material to increase the metal’s anti-corrosion performance and achieve a certain beautification effect. It is a commonly used surface treatment method, such as electrogalvanizing, electronickel plating, etc. Mainly colorful zinc plating, blue and white zinc, black zinc, and chrome plating.
Anodizing
Oxidize the metal on the surface of the workpiece to form a dense protective film on the surface of the workpiece to increase the corrosion resistance of the workpiece. Generally, there are two methods: chemical oxidation and anodizing. It is a commonly used surface treatment method, usually primary color anodizing and black anodizing.
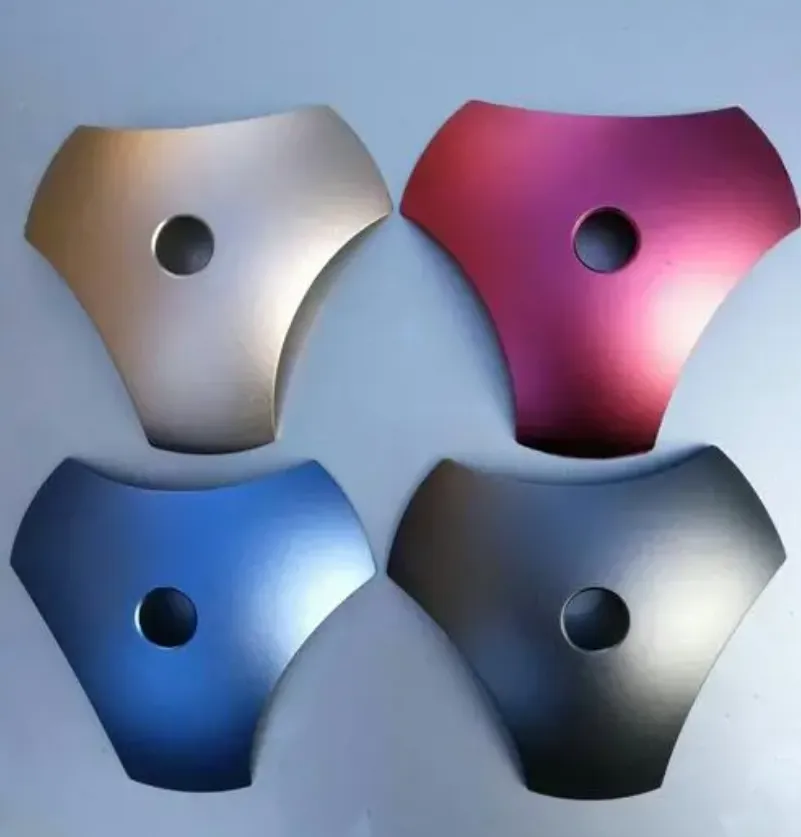
Silkscreen
There are two ways to print various logos on the surface of materials: flat screen printing and pad printing. The main principle is the same as the imaging principle of camera film, which is also an exposure process. Flat screen printing is mainly used on general flat surfaces, but if there are deep pits, pad printing is needed. It is usually used for trademarks, usage logos, warning logos, etc.
Commonly used materials and applications for sheet metal processing
Aluminum alloy : Common grades include 5052, 6061, 7075, etc., which are used in automotive parts, electrical equipment and cookware. It has many advantages, including good strength-to-weight ratio and high conductivity.
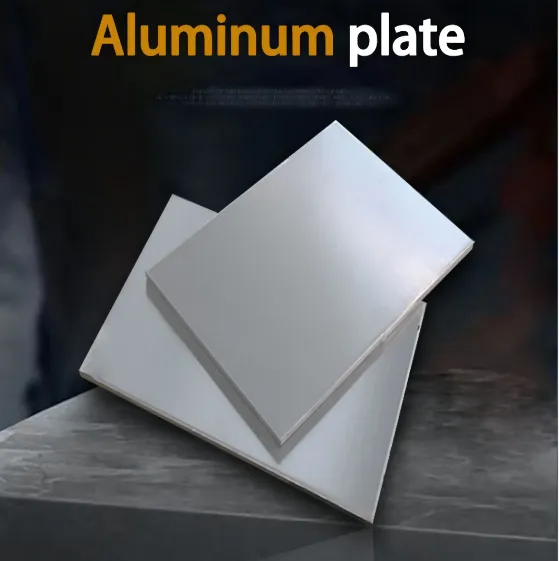
Aluminized Steel: This metal combines the high strength of carbon steel with the superior corrosion resistance of aluminum. Aluminized steel is used for products that are exposed to high temperatures, such as kitchen appliances.
Carbon Steel: Carbon steel is used in a range of products across the industrial and consumer markets. It is a steel alloy that contains carbon, which increases the material’s hardness and strength when heat treated.
Copper: Examples of products made from copper are gutters, roofing, rain gutters, and doors. Copper has higher electrical and thermal conductivity than aluminum, but is also more expensive.
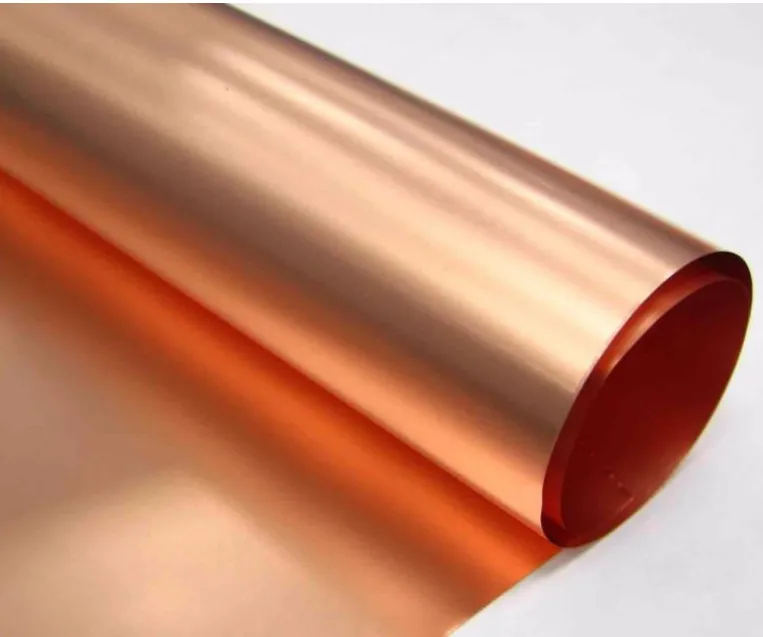
Galvanized Steel: Galvanized steel is often used to make car bodies, water pipes, fences, roofs, and stairs. It is made by coating steel with zinc through a hot-dip process, which helps make it more corrosion-resistant.
High-strength steel: Military armor plates are often made of high-strength steel. The material is made by alloying steel with a range of elements, including carbon, manganese, and copper. This helps increase its hardness.
Stainless steel: Commonly used grades include SUS304/SUS316, etc., which are used in kitchen containers, chemical storage tanks and food processing machinery. Stainless steel has excellent corrosion resistance, fire resistance and heat resistance, strength-to-weight ratio and manufacturability.
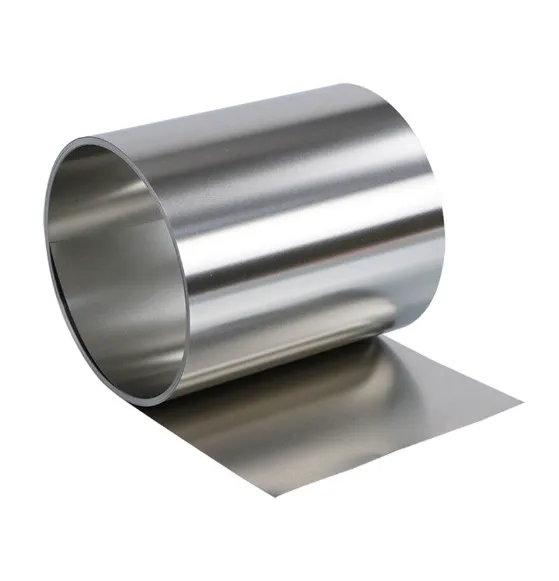
Titanium Alloys: Typical products made from titanium include aerospace parts, medical devices, and architectural elements. It is used primarily for its high strength-to-weight ratio and corrosion resistance.
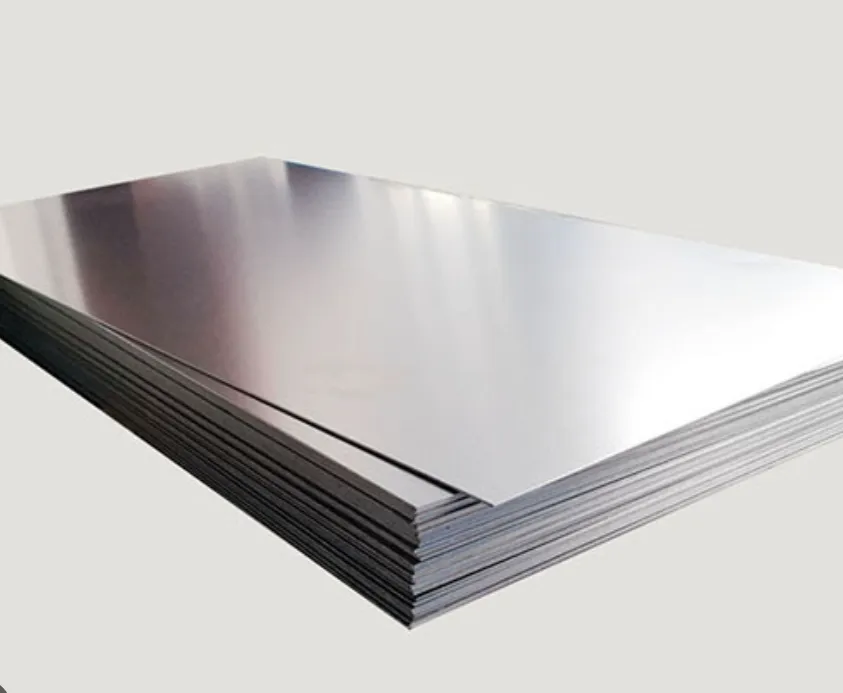
Advantages of sheet metal processing
1.Strong adaptability: Sheet metal processing is particularly suitable for small batch and diversified production, and can meet the customized needs of parts and products of various shapes and sizes.
2.High precision: Using advanced sheet metal processing equipment and technology, high-precision manufacturing can be achieved, providing cost-effective parts with excellent flatness.
3.High efficiency: Sheet metal processing can achieve rapid production and manufacturing, especially after the use of CNC punching machines (NCT), which greatly improves production efficiency.
4.Flexible processing: The cutting technology of sheet metal processing has high speed, high precision and high adaptability, has good shape specifications, and is easy to automatically process.
5.Wide range of applications: Sheet metal processing can be used in CNC equipment and can also meet the needs of automated processing and production
6.Fast delivery cycle: Sheet metal processing has a fast cutting speed and is not limited by the number of processing times. It is particularly suitable for the processing of special-shaped workpieces during the processing, because it does not waste time changing, thereby effectively improving the processing efficiency.