Classification of spraying
The widely used spraying processes are roughly divided into two categories: one is powder spraying, also known as powder coating, which uses plastic powder as the raw material. The other is painting, which applies a paint film on the surface of the workpiece.
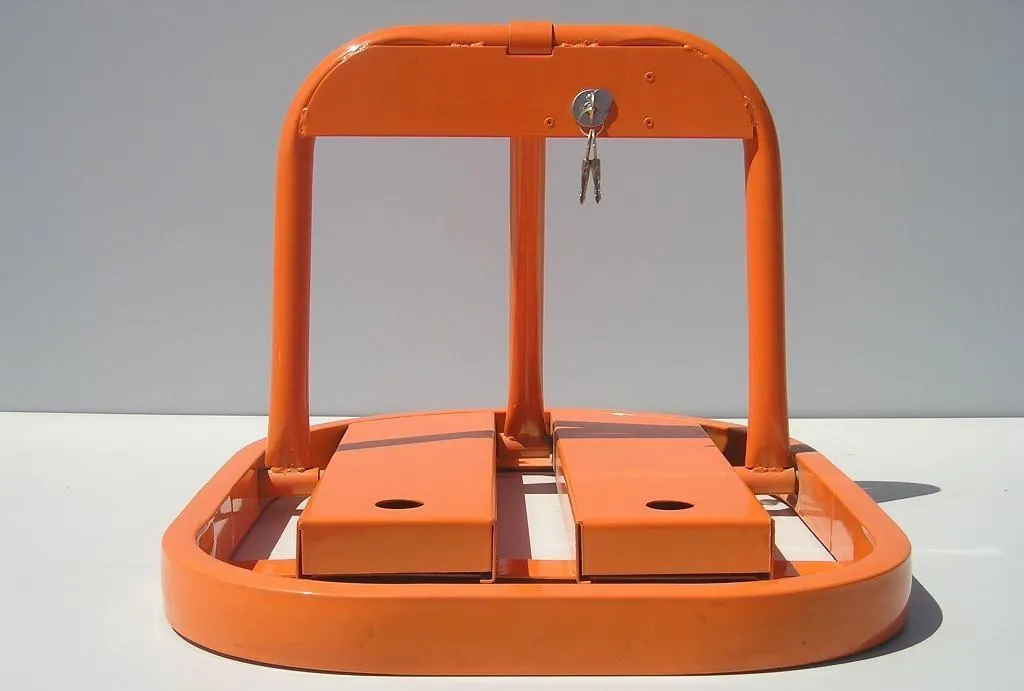
Process principle
01 Powder spraying
A high-voltage corona discharge electric field is formed between the spray gun and the workpiece. When the powder particles are ejected from the spray gun and pass through the discharge area, they gather a large number of electrons and become negatively charged particles. Under the action of electrostatic attraction, they are adsorbed onto the positively charged workpiece. When the powder adheres to a certain thickness, the effect of “like repels like” will occur, and the powder can no longer be adsorbed, so that the thickness of the powder layer in each part is uniform, and then after heating, baking and curing, the powder layer is leveled to form a uniform film layer.
02 Spray paint
Spray painting is a relatively simple surface treatment process, which is done by putting the paint into a container, pressurizing it with a machine, and then spraying the paint onto the product in the form of mist to form a paint film.
Process
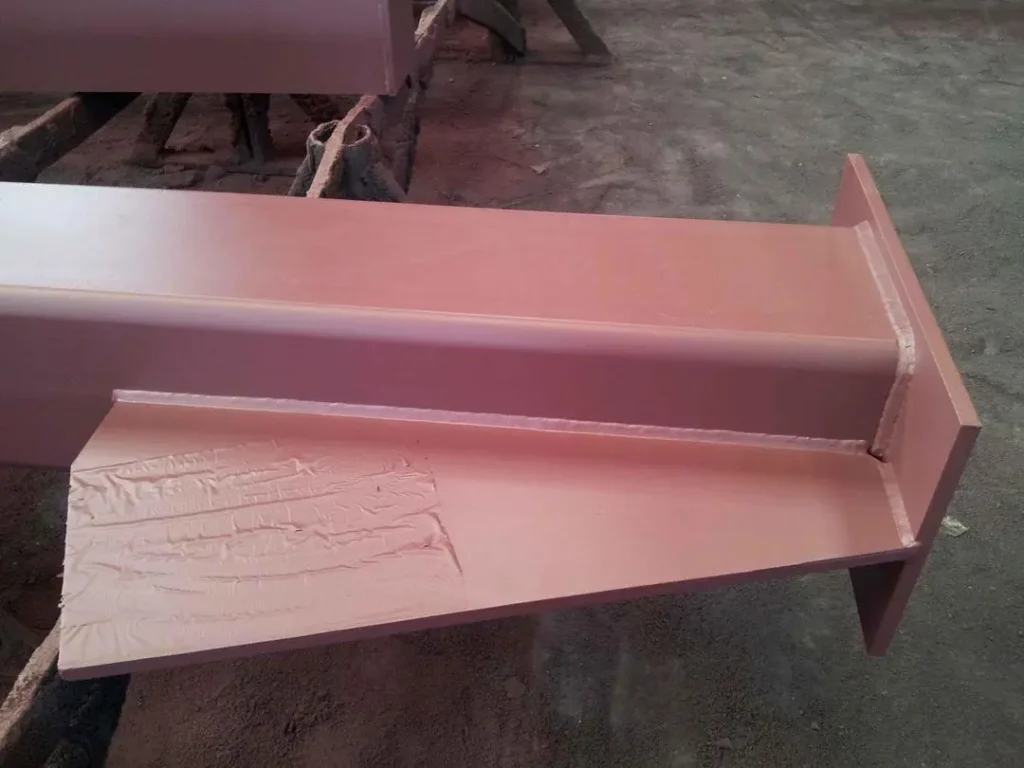
Powder spraying process
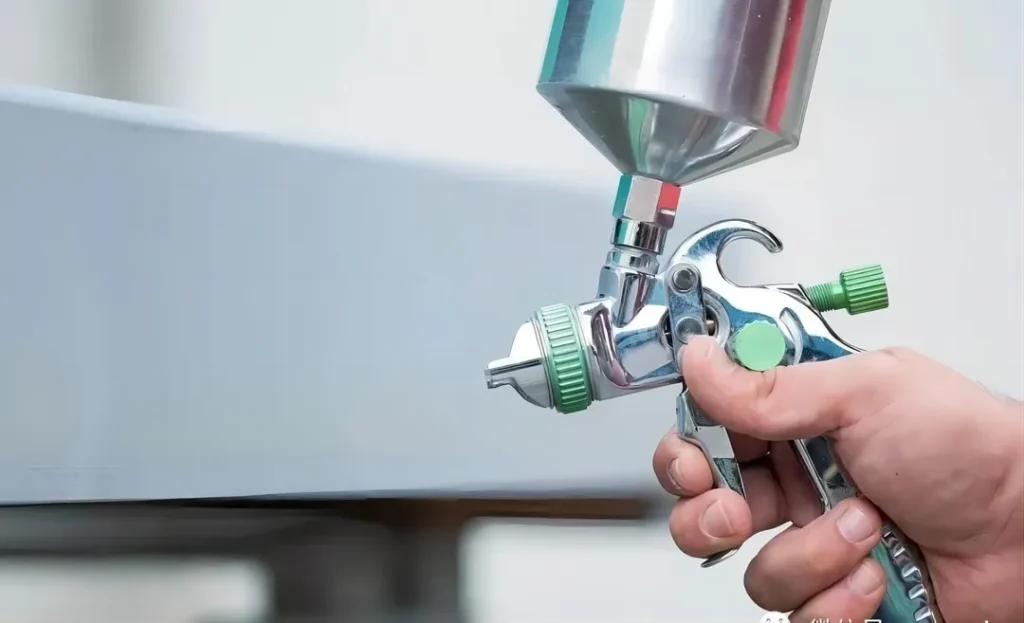
- Load the workpiece and hang it on the powder spraying line;
- Degreasing: the workpiece automatically enters the water washing area and removes the surface oil in the liquid containing the degreasing agent;
- Rust removal (pickling), the workpiece with oil removed enters the pickling area to remove the rust and oxidation layers on the surface, and then cleans after the process is completed;
- Phosphating, so that a phosphating layer is formed on the surface of the workpiece, and then it is cleaned again;
- Powder electrostatic spraying;
- High temperature curing: the coating powder will melt and level itself under high temperature, and finally form a dense and solid spray layer after curing;
- Cool down the parts.
Painting process
- The product also needs to be processed before painting (rust removal (usually shot blasting), degreasing, etc.);
- The treated product must be cleaned and dried naturally before painting;
- Painting can be done by directly spraying a layer of paint, or by repeatedly spraying 2-3 times to obtain a dense and solid paint layer. In the case of multiple spraying, the first spray is also called primer, which must be sanded before the next spraying.
Degreasing, pickling, phosphating
Degreasing
The degreasing process is to remove grease, dirt, etc. on the metal surface to clean the surface of the object. Because the workpiece is easily contaminated with oil stains on the equipment during the molding process, and the oil stains are located on the outermost layer of the workpiece surface, the oil stains must be removed first, which is called degreasing.
Pickling
Then comes pickling, which is the most widely used method for removing rust and scale in the industrial field. The basic principle is to expose the metal surface to a solution containing acidic substances, and use the mechanical stripping effect of acid dissolving oxides and corrosion to produce hydrogen to achieve the purpose of rust and scale removal.
Phosphate
The last step is phosphating. Phosphating is to immerse clean metal in a solution containing phosphoric acid to form a phosphating layer on the metal surface. This phosphating layer can improve the corrosion resistance of the metal surface and increase the adhesion of the metal surface, which is conducive to enhancing the adhesion effect of the coating, thereby improving the final rust and corrosion resistance of the product. It should be noted here that the workpiece must be pre-treated before phosphating to remove grease, rust, oxide scale, etc.
Process characteristics
Powder spraying
Advantage:
(1) A thicker coating can be obtained by one coating. For example, a coating of 100 to 300 ฮผm requires about 4 to 6 coatings with ordinary solvent coatings, while powder coatings can achieve this thickness in one coating. The coating has good corrosion resistance.
(2) Powder coatings do not contain solvents, do not produce three wastes or other public hazards, improve labor hygiene conditions, and cause less harm to the environment and human body.
(3) The coating quality is better and the adhesion is stronger after electrostatic spraying.
(4) Powder electrostatic spraying and other processes are highly efficient, the automatic assembly line coating has a high degree of automation, the powder utilization rate is high, and it can be recycled.
(5) The curing time is short, there will be no liquid dripping, and the finished product has high appearance quality.
Main disadvantages: The plastic-sprayed surface is not easy to repair and the cost is high.
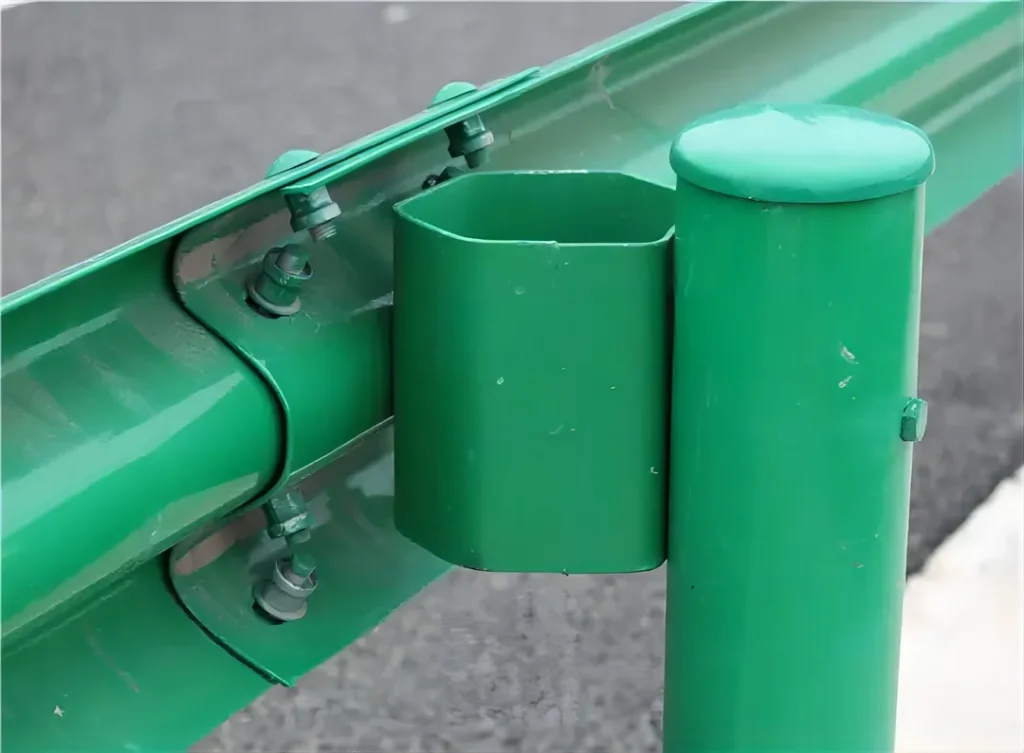
Spray paint
Advantage:
(1) Fast construction speed: Compared with the traditional brushing method, spray painting is faster and can complete large-area painting work in a short time, which is very advantageous for the painting of large projects.
(2) Uniform coating: The spraying method can make the paint evenly cover the surface of the object, with uniform coating thickness and high surface finish.
(3) Can meet the needs of various colors: Spray painting can produce a variety of colors and patterns to meet the needs of different customers. At the same time, the color is bright, the gloss is good, and the color is stable.
(4) Suitable for large-area coating and three-dimensional patterns.
Main disadvantages: A lot of solvent volatilization will be produced during the painting process, which can easily pollute the surrounding environment and cause adverse environmental impacts.
Since corrosion is an irreversible spontaneous process, even a high-quality spray paint retaining layer is difficult to protect metal from corrosion, especially when the spray paint layer on the metal surface is poorly bonded, damaged, or has pinholes, bubbling, cracking, shedding and other defects, the protective effect of the spray paint coating will be greatly reduced, and even cause the metal corrosion to intensify. Therefore, it is very necessary to carefully analyze the corrosion factors of spray paint metal and take effective countermeasures to prevent it.